литье меди под давлением услуга
- Наш процесс литья меди под давлением позволяет изготавливать крупные высокоточные медные детали, независимо от ограничений по материалу, геометрии или толщине стенок.
- Этот метод обеспечивает превосходное качество поверхности, часто делая ненужными дальнейшие процессы отделки.
- Высокая точность и согласованность
- Универсальные методы литья под давлением
- Экономически эффективное производство
- Усовершенствованная отделка поверхности
- Персонализация и гибкость
- Комплексная поддержка и услуги
Процесс литья меди под давлением
Наш процесс литья меди под давлением включает в себя предварительный нагрев форм, плавление и впрыск меди, застывание и тщательное выталкивание, а затем обрезку и полировку для достижения высокой точности.
Подготовка формы
Разработка и создание формы, предварительный нагрев до 200-300°C, обеспечение правильного выравнивания для точного литья и снижения теплового удара.
Плавление и инжекция
Расплавьте медный сплав при температуре 1 085°C и впрысните расплавленный металл в предварительно нагретую форму под высоким давлением (10-175 МПа) для точного придания формы.
Застывание и выталкивание
Охладите отливку в форме, затвердевайте в течение 5-20 секунд, откройте форму и аккуратно извлеките затвердевшую отливку.
Обрезка и отделка
Обрезайте излишки материала, шлифуйте и полируйте для получения требуемой чистоты поверхности, проверяйте на наличие дефектов, обеспечивая точность размеров в пределах ±0,005 дюйма.
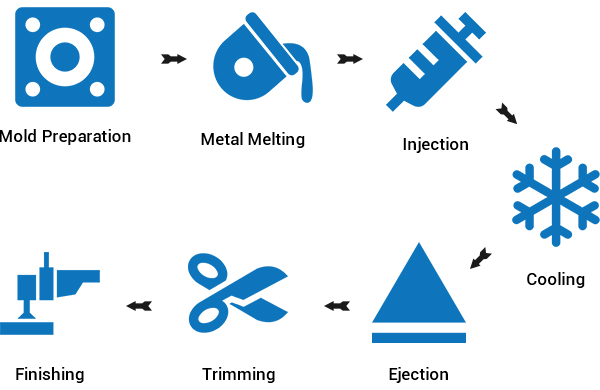
Методы литья меди под давлением
Методы литья меди под давлением включают в себя литье под высоким и низким давлением, литье в холодной камере, гравитационное, центробежное и вакуумное литье, каждое из которых имеет свои уникальные преимущества и сферы применения.
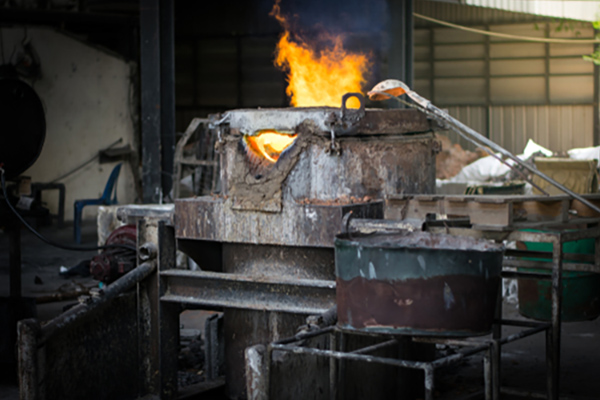
Медное литье под высоким давлением
- Лучше всего подходит для: Сложные формы с жесткими допусками.
- Преимущества: Высокая точность размеров, гладкая поверхность.
- Недостатки: Увеличение расходов на оборудование и эксплуатацию.
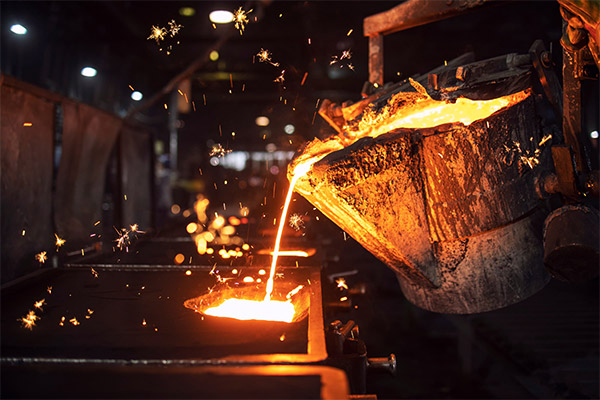
Медное литье под низким давлением
- Лучше всего подходит для: Конструктивные элементы, требующие высокой прочности.
- Преимущества: Лучший контроль над наполнением, уменьшенная пористость, улучшенные механические свойства.
- Недостатки: Более медленный процесс по сравнению с методами высокого давления.
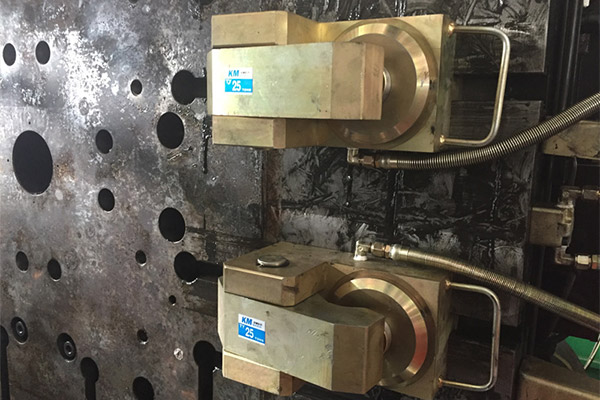
Медное холодное камерное литье под давлением
- Лучше всего подходит для: Металлы с высокой температурой плавления, точные и сложные детали.
- Преимущества: Подходит для меди, высокое давление позволяет создавать замысловатые детали.
- Недостатки: Замедленное время цикла из-за процесса дозирования.
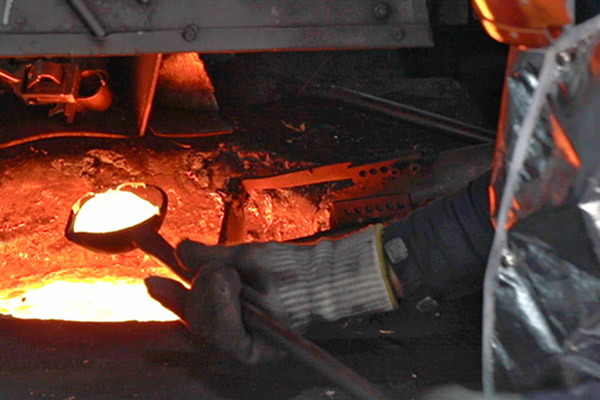
Медное гравитационное литье под давлением
- Лучше всего подходит для: Большие, простые детали с хорошими механическими свойствами.
- Преимущества: Экономичность, подходит для менее сложных деталей.
- Недостатки: Менее подходит для сложных форм.
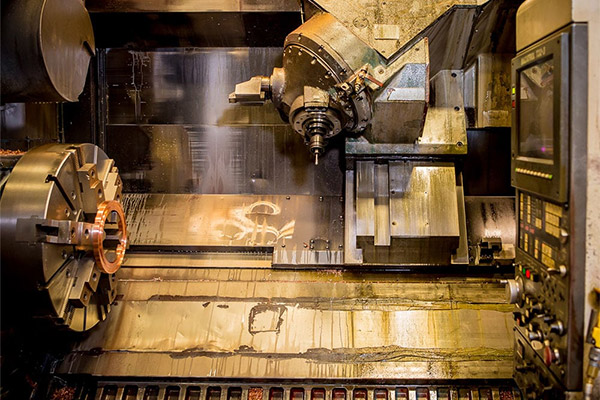
Медное центробежное литье под давлением
- Лучше всего подходит для: Цилиндрические детали, такие как трубы и втулки.
- Преимущества: Высокая плотность деталей, мелкозернистая структура, минимальное количество дефектов.
- Недостатки: Ограничены цилиндрическими формами.
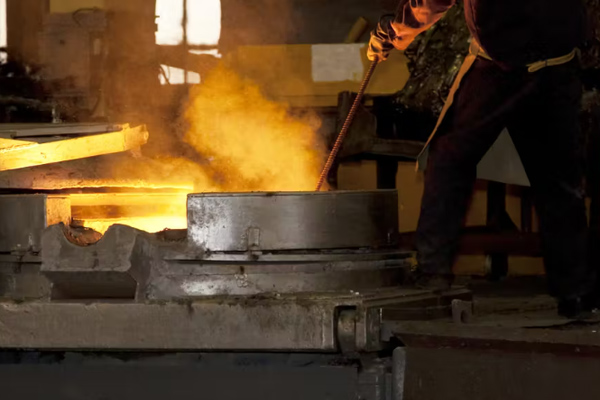
Медное вакуумное литье под давлением
- Лучше всего подходит для: Высококачественные компоненты, требующие минимального количества дефектов.
- Преимущества: Значительно сниженная пористость, повышенная плотность и превосходные механические свойства.
- Недостатки: Увеличение расходов на оборудование и эксплуатацию.
Доступные типы медных сплавов
Типы медных сплавов включают латунь, бронзу, бериллиевую медь, кремниевую бронзу, CuNi и алюминиевую бронзу, каждый из которых обладает уникальными свойствами и областью применения.
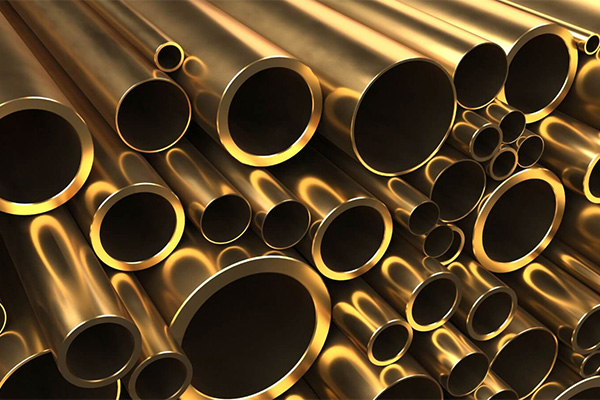
Латунь (медно-цинковые сплавы)
- Модели: C36000, C37700.
- Состав: Cu 60-63%, Zn 35-37%, Pb 2,5-3,7%.
- Характеристики: Отличная обрабатываемость, умеренная прочность, хорошая коррозионная стойкость.
- Области применения: Сантехнические фитинги, электрические разъемы, точные приборы.
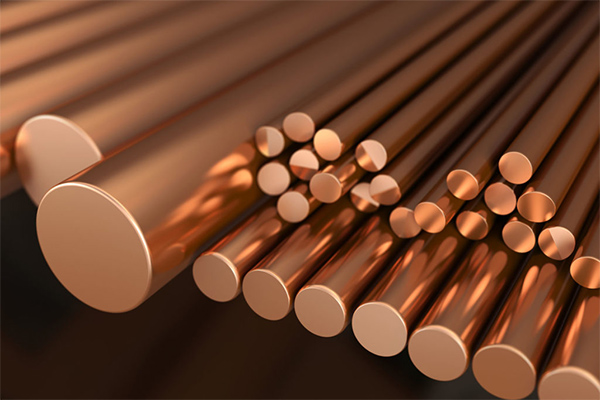
Бронза (медно-оловянные сплавы)
- Модели: C93200, C95400.
- Состав: Cu 81-85%, Sn 6,3-7,5%, Pb 6,0-8,0%.
- Характеристики: Высокая износостойкость, хорошая обрабатываемость, отличная грузоподъемность.
- Области применения: Подшипники, втулки, детали зубчатых колес.
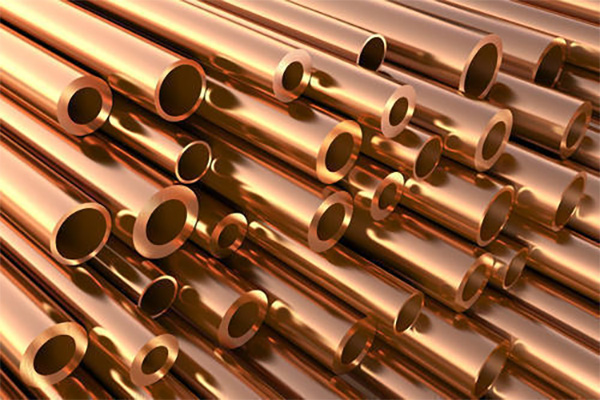
Бериллиевая медь (медно-бериллиевые сплавы)
- Модели: C17200, C17500.
- Состав: Cu 97,9%, Be 1,8-2,0%, Co 0,2%.
- Характеристики: Высокая прочность и твердость, хорошая тепло- и электропроводность, не искрит.
- Области применения: Аэрокосмические компоненты, неискрящие инструменты, электронные разъемы.
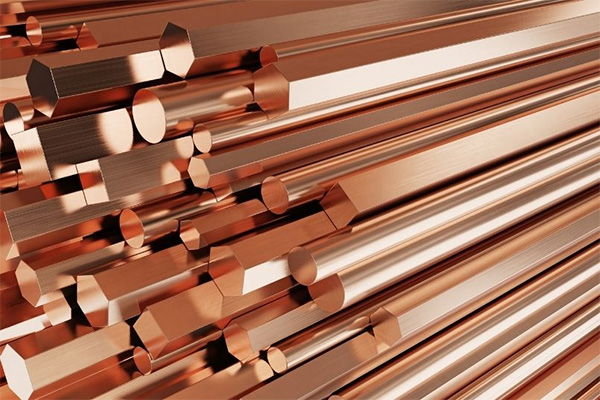
Кремниевая бронза (медно-кремниевые сплавы)
- Модели: C65500, C64200.
- Состав: Cu 96%, Si 2,8-3,8%, Mn 1,5%.
- Характеристики: Отличная коррозионная стойкость, высокая прочность, хорошая свариваемость.
- Области применения: Морское оборудование, оборудование для химической обработки, компоненты насосов и клапанов.
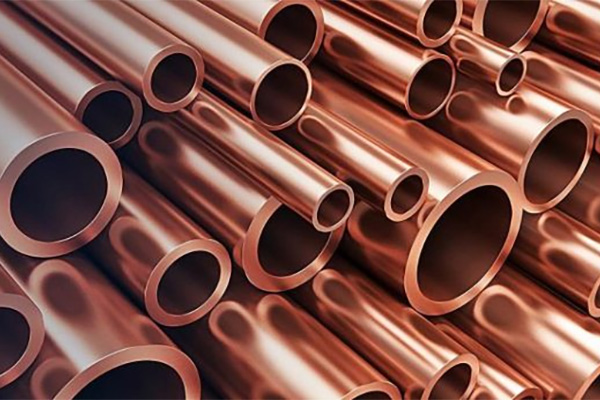
CuNi (медно-никелевые сплавы)
- Модели: C70600, C71500.
- Состав: Cu 69,5-70,5%, Ni 29-30%, Fe 0,4-0,8%.
- Характеристики: Отличная коррозионная стойкость в морской воде, хорошая прочность и пластичность, устойчивость к биообрастанию.
- Области применения: Морская и оффшорная техника, теплообменники, опреснительные установки.
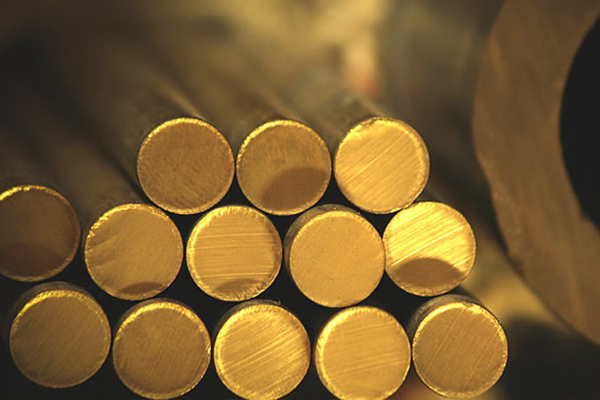
Алюминиевая бронза (медно-алюминиевые сплавы)
- Модели: C95400, C95500.
- Состав: Cu 83,0-87,0%, Al 10,0-11,5%, Fe 3,0-5,0%.
- Характеристики: Высокая прочность и твердость, отличная износостойкость и коррозионная стойкость, хорошая теплопроводность.
- Области применения: Сверхпрочные подшипники, износостойкие пластины, морские гребные винты.
Преимущества и недостатки литья меди под давлением
Изучите преимущества и ограничения литья меди под давлением для промышленного применения, чтобы определить его пригодность для вашего проекта.
Преимущества
- Высокая точность и стабильность.
- Изготавливаемые детали сложной формы.
- Крупносерийное производство.
- Эффективный метод производства.
- Прочные и долговечные компоненты.
- Подходит для различных промышленных применений.
Недостатки
- Легко создает пористость.
- Короткий срок службы штампа.
- Сложный процесс.
- Ограниченная гибкость конструкции.
- Не подходит для малосерийного производства.
Наши проекты по литью меди под давлением
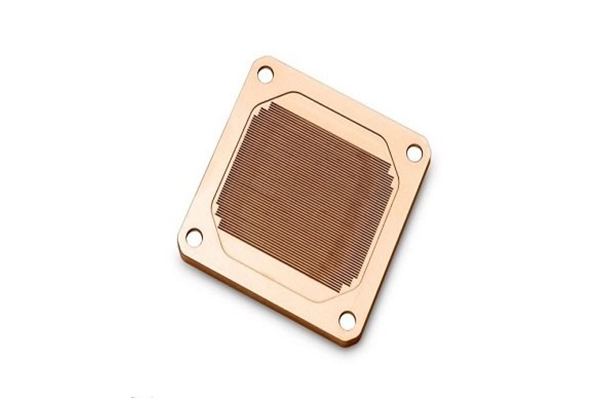
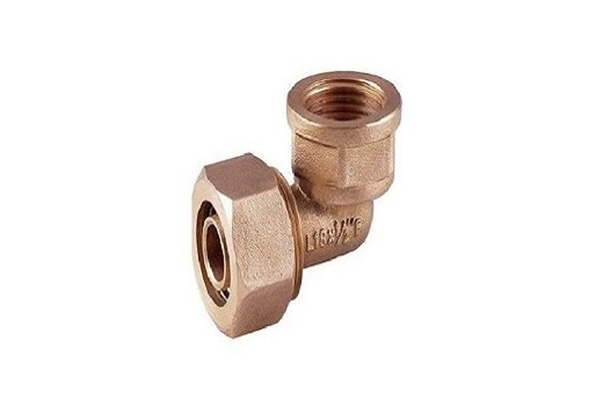
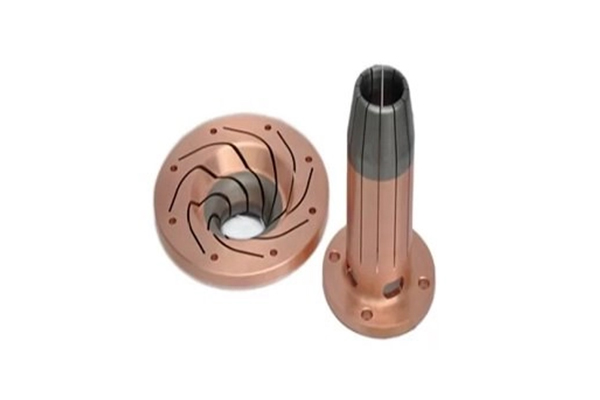
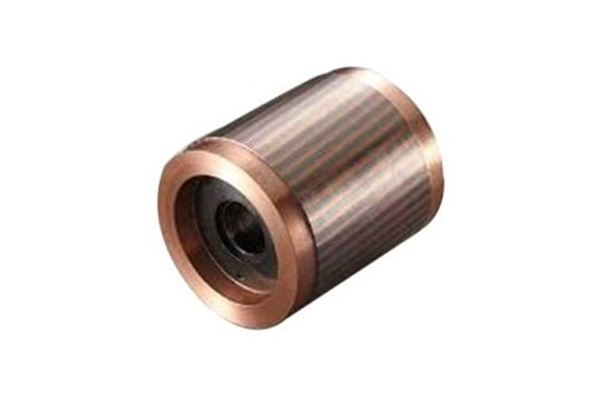
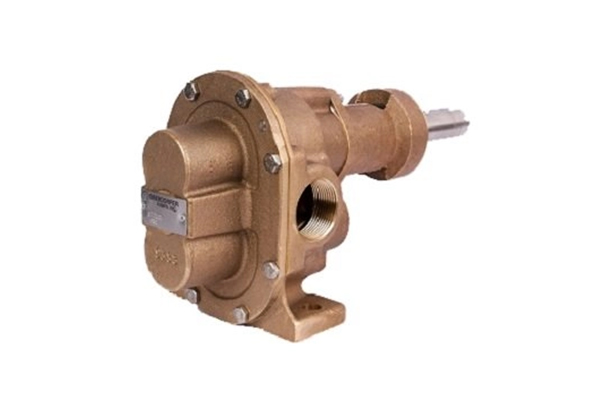
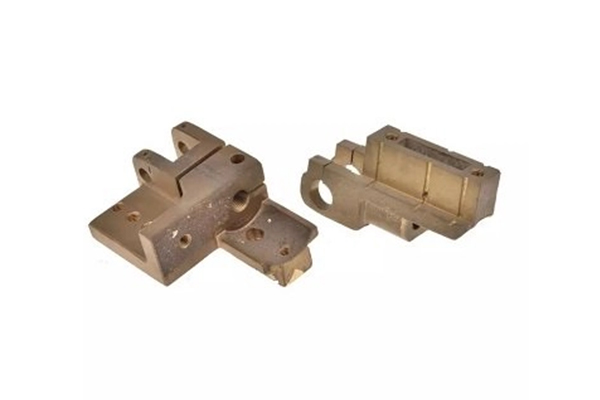
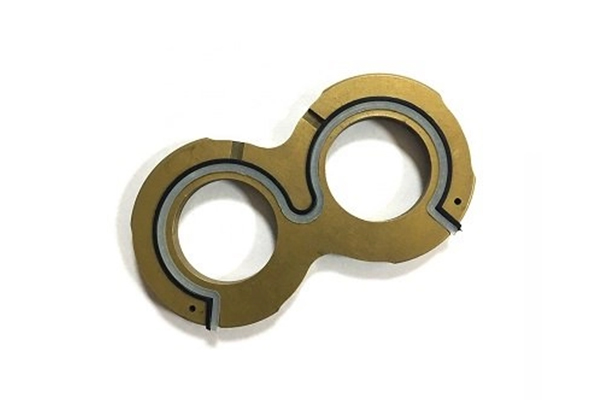
Варианты обработки поверхности
Готовые детали, отлитые под давлением из меди, могут получить различные виды обработки поверхности для повышения долговечности, эстетики и производительности.
- Пассивация
- Пескоструйная обработка
- Порошковое покрытие
- Полировка
- Термообработка
- Покрытие
- Анодирование
- Химическое конверсионное покрытие
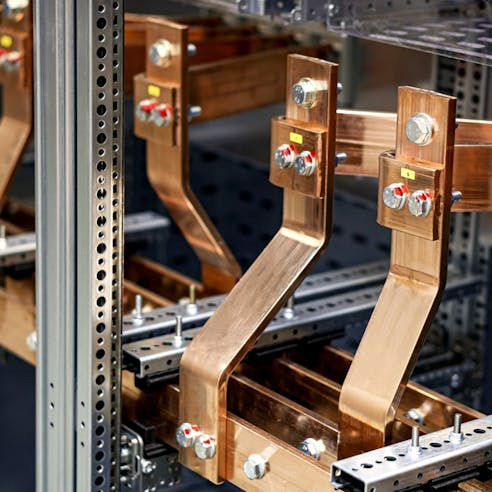
Популярные вопросы
Какие области применения выигрывают от процесса литья латуни под давлением?
Области применения, в которых используется процесс литья латуни под давлением, включают сантехническую арматуру, электрические компоненты и автомобильные детали, для которых важны долговечность и точность.
Какие отрасли промышленности выигрывают от литья под давлением медных роторов?
Такие отрасли, как автомобилестроение, промышленное оборудование и энергетика, выигрывают от литья под давлением медных роторов благодаря их эффективности, долговечности и улучшенным характеристикам двигателя.
Что такое гравитационное литье латуни?
Литье латуни под давлением предполагает заливку расплавленной латуни в форму под действием силы тяжести. Этот метод позволяет получать высококачественные детали с отличными прочностными и поверхностными характеристиками, подходящие для различных промышленных и декоративных применений.
Как повысить экономическую эффективность литья латуни под давлением?
Литье латуни под давлением является экономически эффективным для крупносерийного производства. Она обеспечивает высокую точность и минимальное количество отходов, что делает ее экономичным выбором для изготовления деталей.
Почему стоит выбрать литье латуни или бронзы?
Выбирайте латунное литье для электрических и сантехнических деталей благодаря его прочности и электропроводности. Для деталей, требующих высокой коррозионной стойкости и долговечности, например, в морской и промышленной промышленности, выбирайте бронзовое литье под давлением.
Какие преимущества дает процесс литья меди под давлением?
Процесс литья меди под давлением обеспечивает высокую прочность, отличную тепло- и электропроводность, а также исключительную точность. Он идеально подходит для производства сложных и прочных компонентов, используемых в различных отраслях промышленности.