Servicio de fundición a presión personalizado
- Nuestro servicio de fundición a presión se destaca en la producción de grandes volúmenes de componentes precisos con geometrías complejas y tolerancias estrictas.
- Utilizando técnicas avanzadas, logramos acabados superficiales superiores directamente desde el molde, minimizando la necesidad de soluciones de mecanizado adicionales.
- Diversos tipos de procesos de fundición a presión
- Tolerancia: ±0,127 mm ~ ±0,038 mm
- Alta eficiencia de producción
- Geometrías complejas
- Espesores de pared variables
- Diversos tratamientos de superficie
- Reducción de desechos
Pasos comunes de la fundición a presión
El proceso de fundición a presión crea componentes metálicos complejos inyectando metal fundido en moldes de precisión, produciendo piezas de alta calidad con excelente precisión.
Preparación del molde
Clean, lubricate, and securely clamp the die mold to withstand high-pressure injection.
Fusión de metales
Calentar el metal elegido en un horno hasta que se licue.
Inyección
Inyectar metal fundido en la cavidad de la matriz a alta presión para rellenar detalles intrincados.
Enfriamiento
Deje que el metal fundido se enfríe y se solidifique, moldeándose a la forma de la cavidad de la matriz.
Ejection
Abra el molde y utilice pasadores expulsores para liberar la pieza fundida solidificada.
Guarnición
Retire el exceso de material (rebaba) de la pieza fundida mediante procesos de recorte manuales o automatizados.
Refinamiento
Inspeccione la pieza fundida para verificar su calidad y precisión dimensional, y realice cualquier operación de acabado necesaria.
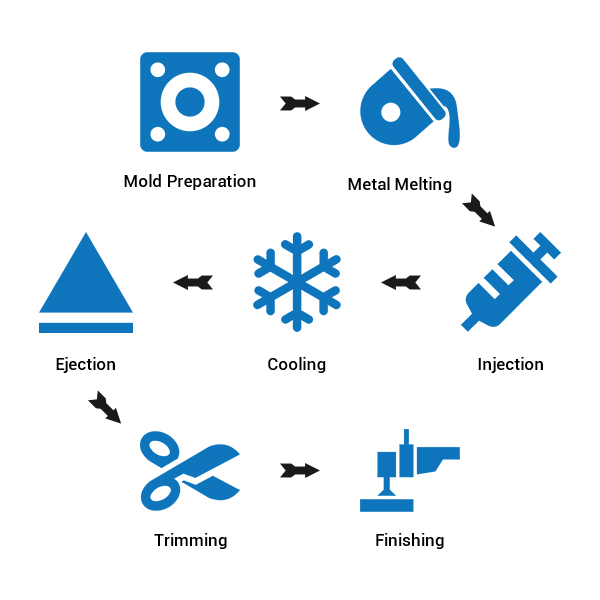
Tipos de procesos de fundición a presión
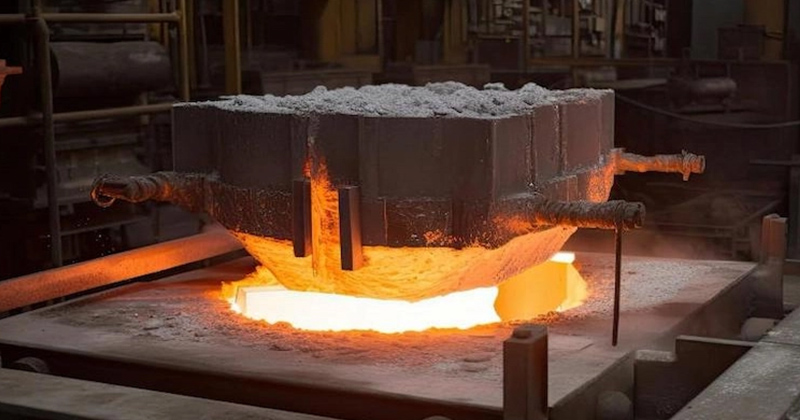
Fundición a presión en cámara caliente
- Cámara de fusión integrada: ciclos rápidos e inyección de metal eficiente.
- Presiones de inyección: 1.500 a 4.500 psi.
- Precisión: ±0,127 mm.
- Alcance: Ideal para metales de bajo punto de fusión como zinc y magnesio en automóviles, productos electrónicos y pequeñas piezas mecánicas.
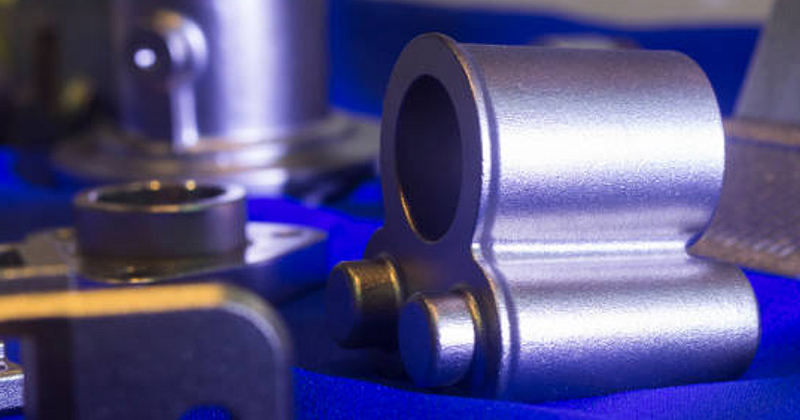
Fundición a presión en cámara fría
- Horno separado para fundir:Metales con punto de fusión más elevado.
- Presiones de inyección: 3.000 a 10.000 psi.
- Precisión: ±0,127 mm.
- Alcance: Ideal para metales como aluminio, latón y bronce, utilizados en la industria automotriz, aeroespacial y piezas estructurales de gran tamaño.
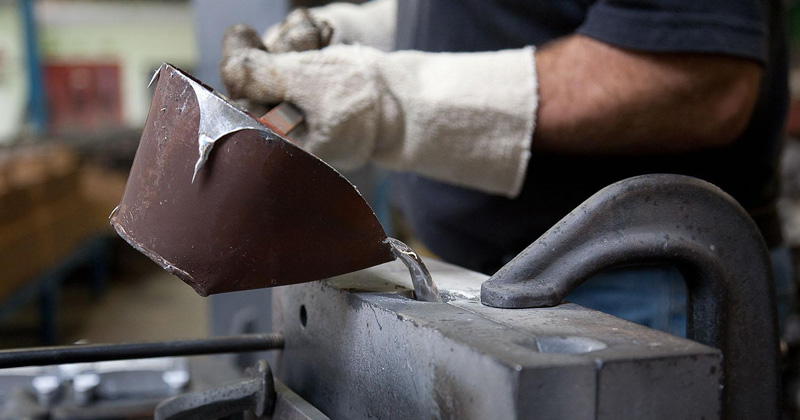
Fundición a presión por gravedad (GDC)
- Proceso de llenado natural: llena la cavidad del molde mediante el uso de la gravedad.
- Presiones de inyección: Sin presión externa; depende únicamente de la gravedad.
- Precisión: ±0,25 a ±0,50 mm.
- Alcance: Ideal para piezas de fundición de tamaño mediano a grande con geometrías simples.

Fundición a presión al vacío
- Evacuación de aire: Reduce la porosidad del gas.
- Presiones de inyección: varían según el metal y el diseño.
- Precisión: ±0,02 a ±0,05 mm.
- Alcance: Componentes automotrices, aeroespaciales y electrónicos de alta integridad.

Fundición a presión
- Combina fundición a presión y forja: solidificación a alta presión para piezas densas.
- Presiones de inyección: Hasta 10.000 psi.
- Precisión: ±0,127 mm.
- Ámbito de aplicación: Suspensión de automóviles, piezas de aeronaves, piezas mecánicas de alta resistencia.
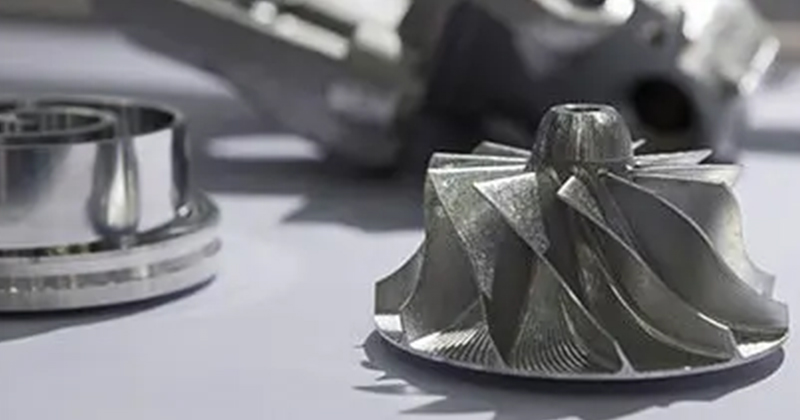
Fundición a presión semisólida
- Utiliza metal semisólido: mejora la precisión y reduce la contracción.
- Presiones de inyección: 1.500 a 4.000 psi.
- Precisión: ±0,01 mm.
- Alcance: Geometrías complejas en automoción, aeroespacial, piezas de alta precisión.
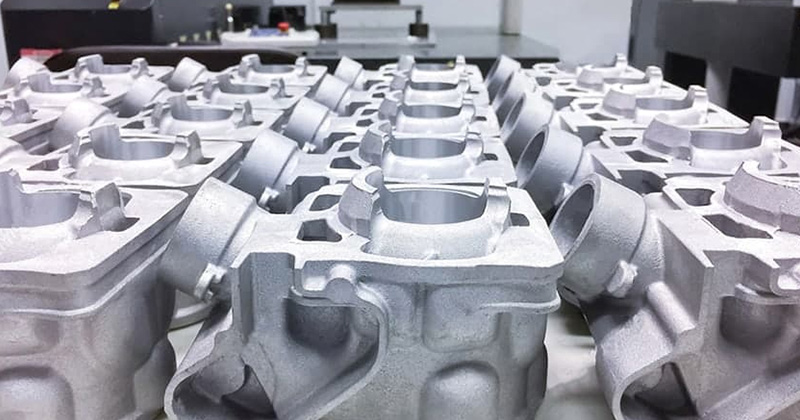
Fundición a presión a baja presión
- Llenado a baja presión: 1-2 bar, reduce defectos.
- Materiales comunes: Aluminio, aleaciones de magnesio.
- Precisión: ±0,1 mm.
- Ámbito de aplicación: Ruedas de automóviles, componentes estructurales, piezas de carcasas de gran tamaño.
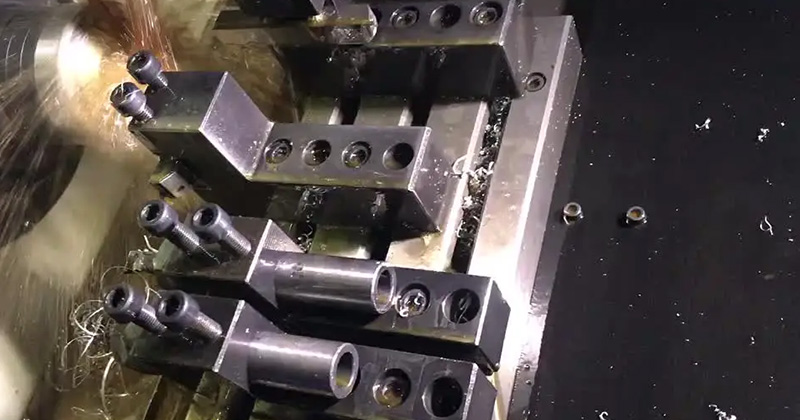
Fundición a presión a alta presión
- Inyección a alta presión: el metal fundido se inyecta en la cavidad de un molde a presiones muy altas.
- Presiones de inyección: 10.000 a 30.000 psi.
- Precisión: ±0,05 mm.
- Alcance: Ideal para la producción de grandes volúmenes de piezas complejas y de paredes delgadas.
Materiales metálicos disponibles
Explore las características y aplicaciones de varios materiales de fundición a presión, incluidos aluminio, zinc, magnesio, cobre y otras aleaciones en diferentes industrias.
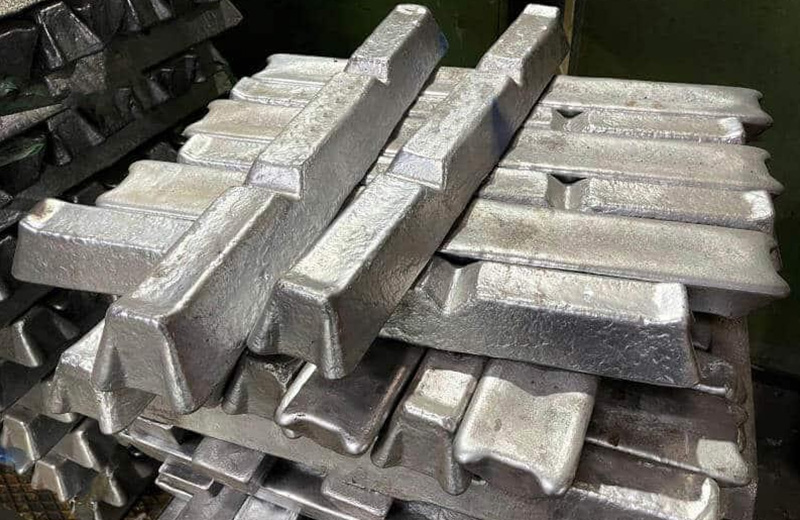
Aleaciones de aluminio
- Modelo: A380, A360, A356, A383, ADC12.
- Punto de fusión: 660,3°C.
- Alta resistencia: resistencia a la tracción típicamente 310 MPa (A380).
- Conductividad térmica: 96-136 W/mK, ideal para disipación de calor.
- Aplicaciones: Su resistencia a la corrosión lo hace adecuado para piezas automotrices, aeroespaciales, electrónicas y estructurales.
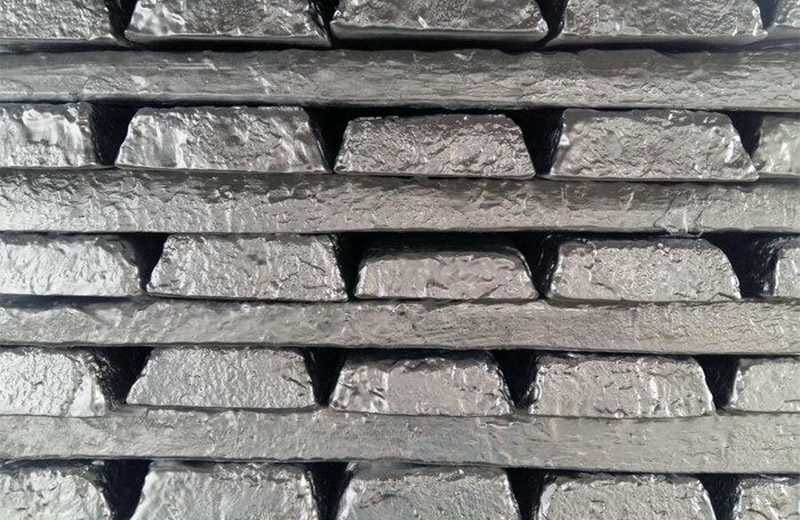
Aleaciones de zinc
- Modelo: Zamak 3, Zamak 5, Zamak 7.
- Punto de fusión: 419,5°C.
- Alta ductilidad: Alargamiento de rotura 10-15%, para formas complejas.
- Resistencia al desgaste: Dureza alrededor de 82 Brinell (Zamak 3).
- Aplicaciones: La conductividad eléctrica del 27 % IACS es ideal para piezas electrónicas, de hardware, automotrices y decorativas.
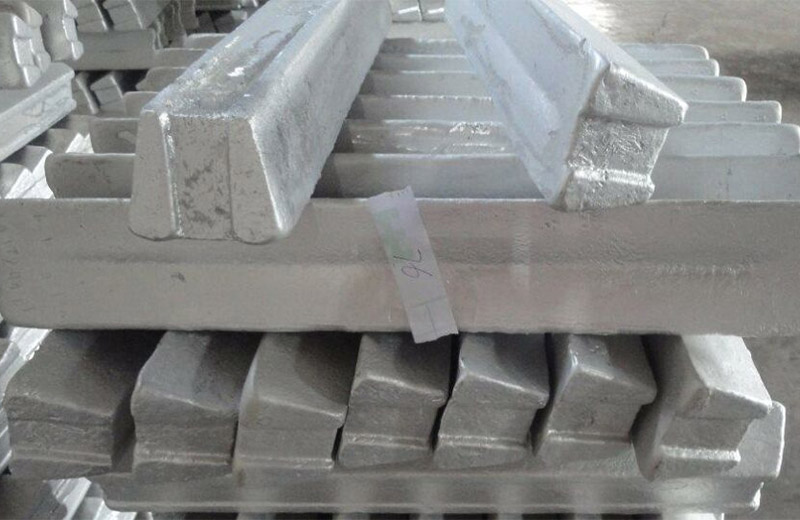
Aleaciones de magnesio
- Modelo: AZ91D, AM60B, AS41B.
- Punto de fusión: 650°C.
- Alta relación resistencia-peso: Resistencia a la tracción 230 MPa (AZ91D).
- Buena maquinabilidad: Velocidades de mecanizado 2,5 veces más rápidas que el aluminio.
- Aplicaciones: El blindaje EMI lo hace adecuado para la industria automotriz, aeroespacial, dispositivos portátiles y artículos deportivos.
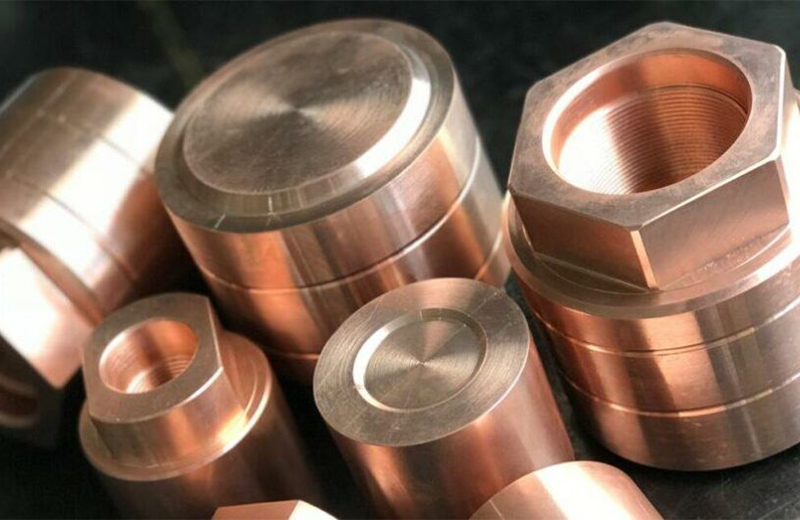
Aleaciones de cobre
- Modelo: C84400, C84800.
- Punto de fusión: 1.085°C.
- Alta resistencia: resistencia a la tracción alrededor de 310 MPa (C84400).
- Resistencia a la corrosión: Excelente en diversos entornos.
- Aplicaciones: Su alta resistencia al desgaste es adecuada para componentes eléctricos, de plomería, industriales y marinos.
Tratamiento de superficies
El tratamiento de superficies en fundición a presión implica varios procesos para mejorar las propiedades y el rendimiento de las piezas de metal fundido.
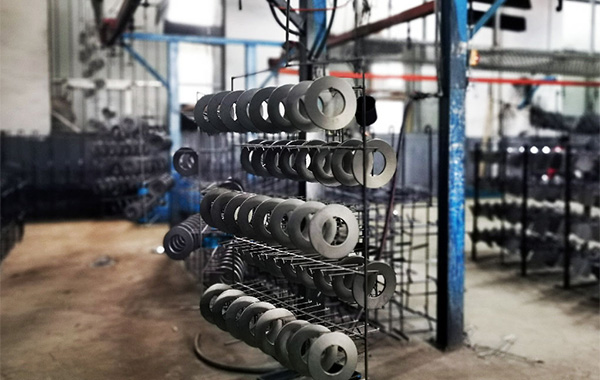
Galvanoplastia
- Propósito: Proporciona una capa decorativa y protectora.
- Beneficios: Mejora la resistencia a la corrosión, la resistencia al desgaste y la apariencia.
- Materiales utilizados: Cromo, níquel, zinc.
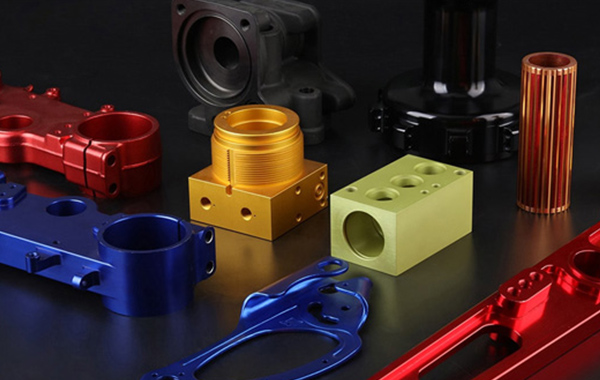
Anodizado
- Propósito: Crea una capa gruesa de óxido en la superficie.
- Beneficios: Mejora la resistencia a la corrosión, la dureza de la superficie y la retención del tinte para colorear.
- Materiales utilizados: Principalmente aleaciones de aluminio.
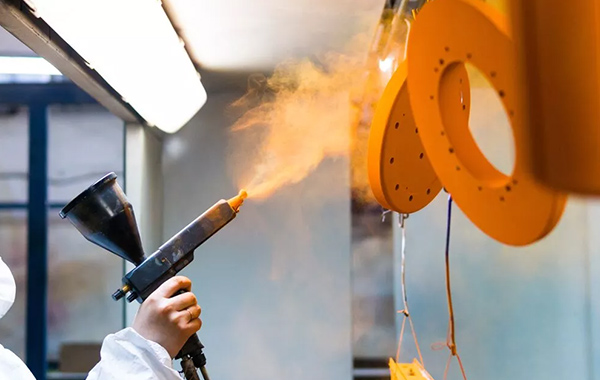
Recubrimiento en polvo
- Propósito: Proporciona una capa protectora y decorativa.
- Beneficios: Proporciona un acabado duradero, uniforme y atractivo con buena resistencia a la corrosión.
- Materiales utilizados: Polvo de polímero termoplástico o termoendurecible.
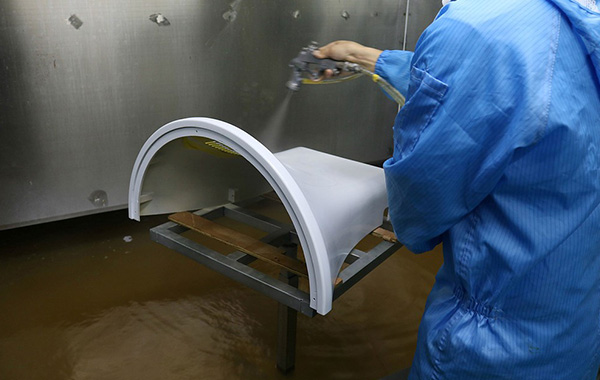
Cuadro
- Propósito: Añade una capa protectora y estética.
- Beneficios: Mejora la apariencia, ofrece resistencia a la corrosión y permite la personalización del color.
- Materiales utilizados: Pinturas acrílicas, epoxicas, poliuretano.
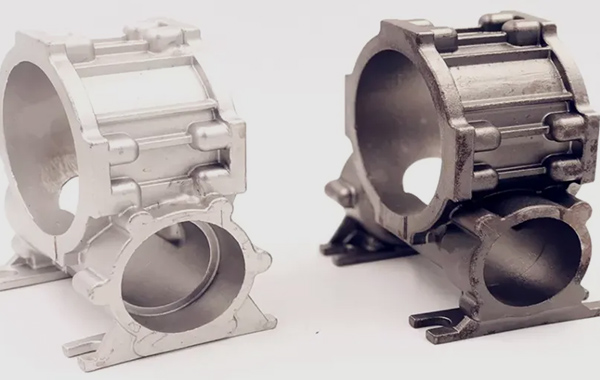
Pasivación
- Propósito: Aumenta la resistencia a la corrosión de las superficies metálicas.
- Beneficios: Produce una capa de óxido protectora y elimina impurezas.
- Materiales utilizados: Soluciones de ácido nítrico o ácido cítrico.
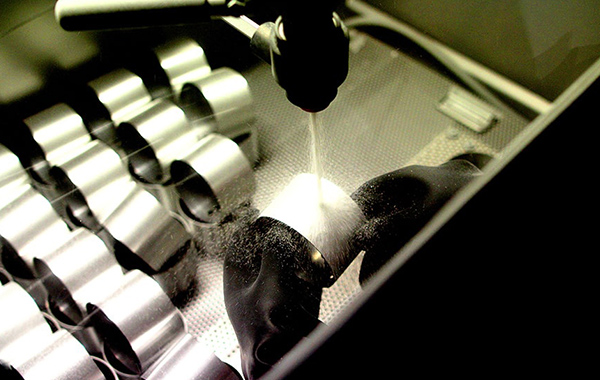
Chorro de arena
- Propósito: Limpia y rugosa la superficie para una mejor adherencia de los recubrimientos.
- Beneficios: Mejora la limpieza de la superficie y la adherencia de recubrimientos posteriores.
- Materiales utilizados: Materiales abrasivos como arena, perlas de vidrio, óxido de aluminio.
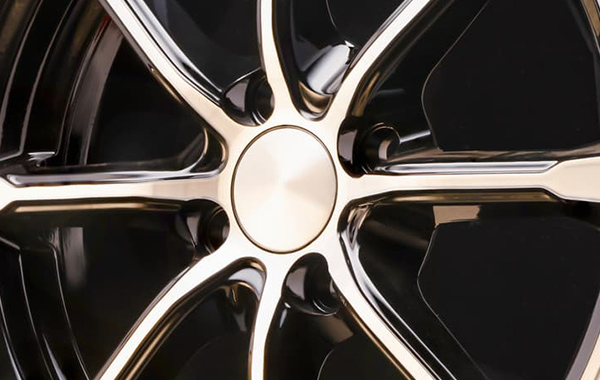
Pulido
- Propósito: Crea un acabado de superficie suave y brillante.
- Beneficios: Mejora la apariencia y reduce la rugosidad de la superficie.
- Materiales utilizados: Compuestos abrasivos y ruedas de pulido.
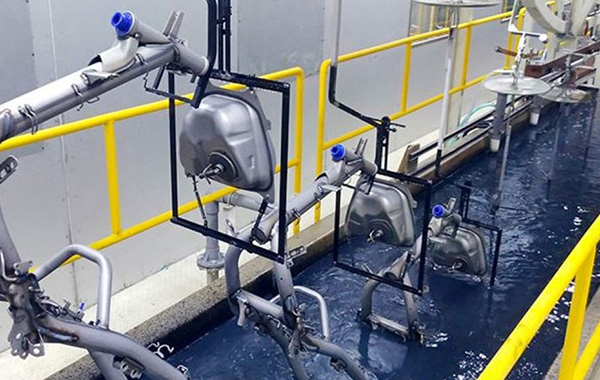
Recubrimiento electroforético (pintura electroforética)
- Propósito: Aplica una capa protectora fina y uniforme.
- Beneficios: Proporciona una excelente resistencia a la corrosión y un espesor de recubrimiento uniforme.
- Materiales utilizados: Partículas de pintura cargadas eléctricamente.
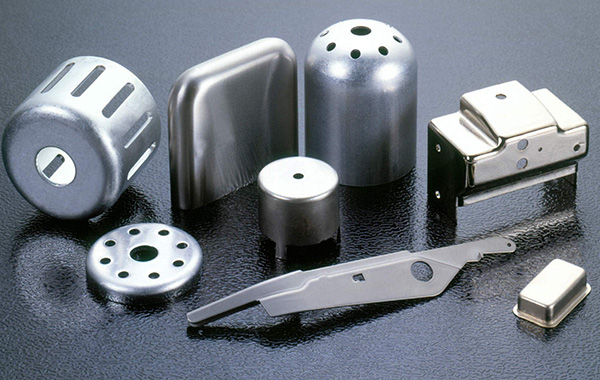
Recubrimiento de conversión de cromato
- Propósito: Proporciona resistencia a la corrosión y una base para la pintura.
- Beneficios: Mejora la resistencia a la corrosión y la adhesión de la pintura.
- Materiales utilizados: Compuestos de cromato, adecuados para aleaciones de aluminio y zinc.
Nuestros proyectos de fundición a presión
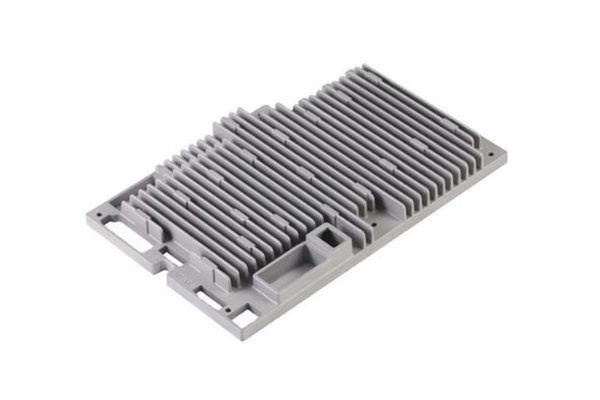
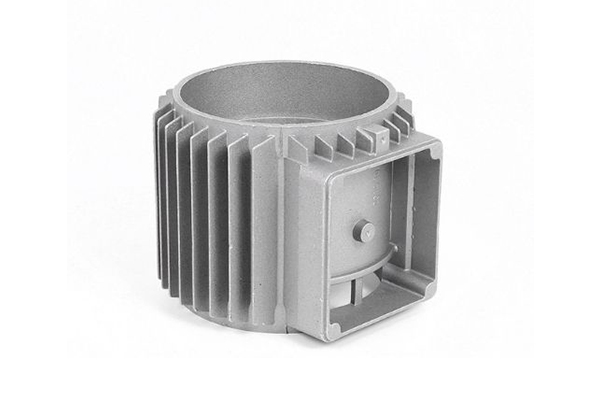
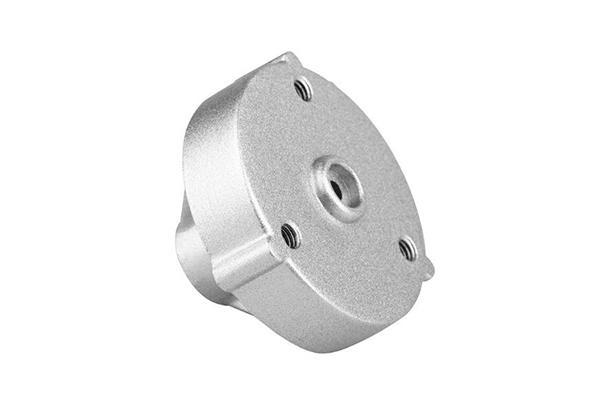
Aplicaciones de fundición a presión
La fundición a presión es un proceso versátil que se utiliza en distintas industrias para producir componentes ligeros, precisos y de alta resistencia.
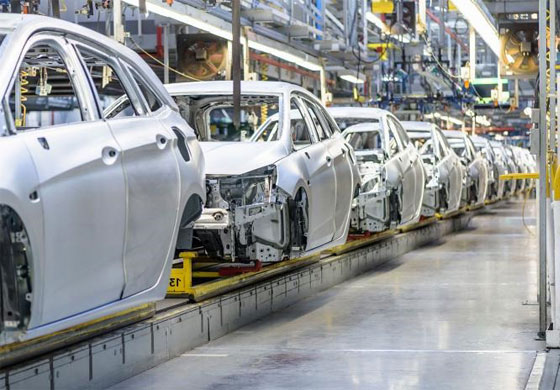
Industria automotriz
La fundición a presión produce componentes de motor, piezas de transmisión, soportes y carcasas, ofreciendo componentes de alta resistencia, livianos y precisos esenciales para mejorar el rendimiento y la eficiencia del combustible.
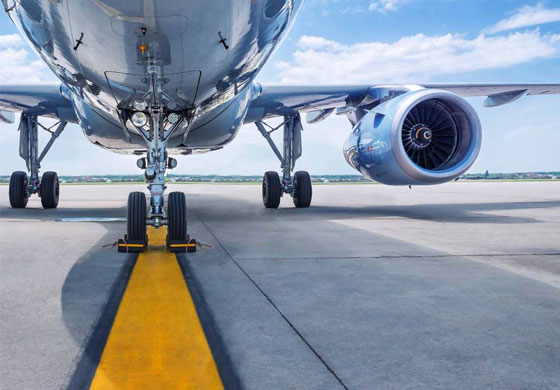
Industria aeroespacial
En la industria aeroespacial, la fundición a presión crea piezas de motor, componentes estructurales y carcasas de instrumentación con formas complejas para cumplir con estrictos estándares de rendimiento y seguridad.
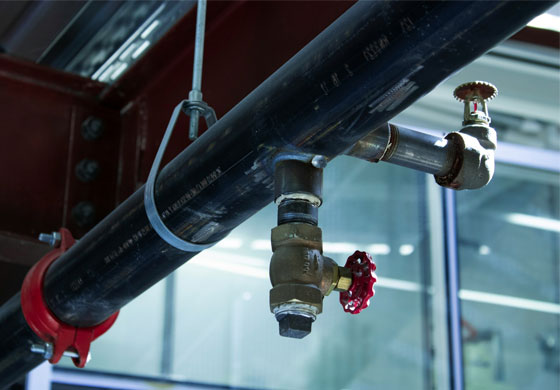
Maquinaria industrial
La fundición a presión se utiliza en maquinaria industrial para componentes de bombas, cuerpos de válvulas y carcasas de cajas de engranajes, lo que garantiza una alta durabilidad, precisión y rentabilidad.

Dispositivos médicos
Para los dispositivos médicos, la fundición a presión fabrica carcasas de equipos de diagnóstico y componentes de equipos de imágenes, brindando la alta precisión y las geometrías complejas necesarias para cumplir con los estrictos estándares médicos.
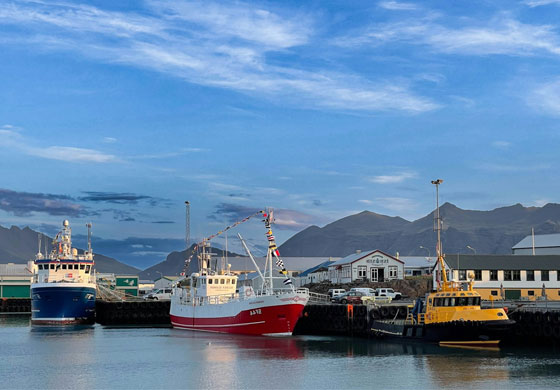
Industria Marina
La fundición a presión se utiliza para producir componentes de motores de barcos, piezas estructurales y accesorios para embarcaciones marinas resistentes a la corrosión, lo que garantiza la robustez en entornos hostiles de agua salada.
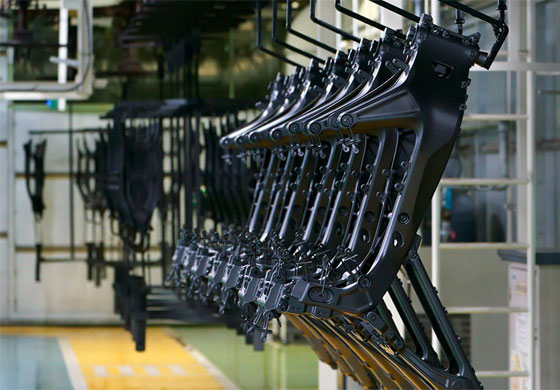
Artículos deportivos
La fundición a presión fabrica componentes de bicicletas livianos y resistentes, piezas de equipos de fitness y equipos para exteriores duraderos, mejorando la longevidad en diversas aplicaciones deportivas.
Preguntas frecuentes
¿Cuál es el espesor de pared mínimo típico que se puede lograr en la fundición a presión?
El espesor de pared mínimo típico para la fundición a presión varía de 0,5 a 2,0 mm, dependiendo del material y del proceso de fundición a presión específico utilizado.
¿Cómo se compara la fundición a presión de zinc con la del aluminio y el latón?
La fundición a presión de zinc permite paredes más delgadas y detalles más finos, con puntos de fusión más bajos y ciclos de producción más rápidos en comparación con el aluminio y el latón.
¿Cuáles son los principales desafíos de la fundición a presión en cámara fría y caliente?
Los desafíos de la cámara caliente incluyen limitaciones de material debido a los bajos puntos de fusión, mientras que los desafíos de la cámara fría implican tiempos de ciclo más largos y maquinaria más compleja.
¿En qué se diferencia la fundición por gravedad de aluminio de la fundición a presión?
La fundición por gravedad generalmente produce menos porosidad y mejores propiedades mecánicas, aunque puede tener tasas de producción más lentas y ser menos adecuada para formas complejas en comparación con la fundición a presión.
¿Cuáles son las aplicaciones comunes de la fundición a presión de alta precisión?
Las aplicaciones comunes incluyen componentes de motores, carcasas de dispositivos médicos, conectores electrónicos, piezas aeroespaciales y herramientas de precisión.
¿Qué aleaciones se utilizan normalmente en la fundición a presión de acero inoxidable?
Las aleaciones comunes incluyen 304, 316 y 17-4 PH, seleccionadas por sus propiedades mecánicas específicas y resistencia a la corrosión.
¿Qué estándares de calidad se siguen normalmente en CQS Precision Die Casting?
En la fundición a presión de precisión CQS se suelen seguir estándares de calidad como ISO 9001, IATF 16949 (para automoción) y AS9100 (para aeroespacial) para garantizar los más altos niveles de calidad y consistencia.
¿Cómo funciona la fundición a presión con núcleo de sal?
El proceso consiste en colocar un núcleo de sal preformado dentro del molde de fundición a presión. A continuación, el molde que contiene el núcleo de sal se llena con metal fundido. Una vez que el metal se solidifica, el núcleo de sal se disuelve con agua o un disolvente adecuado, dejando la cavidad interna o la estructura compleja dentro de la pieza metálica.